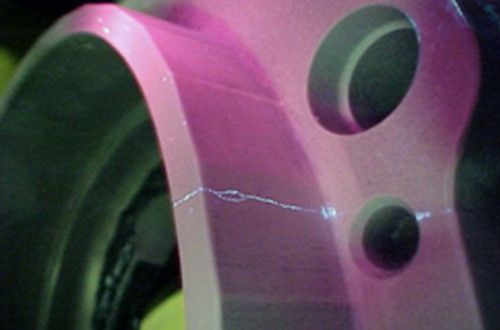
Penetrant Testing (PT)
Dye penetrant inspection (DPI), also called liquid penetrant inspection (LPI) or penetrant testing (PT), is a widely applied and low cost inspection method used to locate surface-breaking defects in non-porous materials (metals, plastics or ceramics).
LPI is used to detect casting, forging and welding surface defects such as hairline cracks, surface porosity, leaks in new products, and fatigue cracks on in-service components.
DPI is based upon capillary action, where low surface tension fluid penetrates into clean and dry surface-breaking discontinuities. Penetrant may be applied to the test component by dipping, spraying, or brushing. After adequate penetration time has been allowed, the excess penetrant is removed and a developer is applied. The developer helps to draw penetrant out of the flaw where a visible indication becomes visible to the inspector. Inspection is performed under ultraviolet or white light, depending upon the type of dye used - fluorescent or nonfluorescent.
- - Wheels
- - Stringers
- - Engine blades for the detection of cracks, corrosion and wear
- - Gears for grinding cracks, wear, and fatigue induced defects
- - Door latches for wear and cracks
- - Wing attach pins for exfoliation corrosion
- - Bolts cracks and corrosion
- - Aircraft skins for crack length verification prior to and post stop drilling a crack
- - Blended areas post corrosion removal
- - Bird strike damage evaluation and verification
- - Blended blade verification
- - Lightning strike
- - Landing gear hard landing inspection
- - Hydraulic system crack detection
- - Wheel bolts testing